At Soleos Energy Private Limited, we believe the future is solar. As global energy needs rise and the call for sustainability grows louder, solar module manufacturing stands at the heart of the green revolution. Solar modules—often referred to as solar panels—are the core component that converts sunlight into usable electricity.
Table of Contents
In this in-depth blog, we walk you through the complete journey of solar module manufacturing—from raw materials to a high-performing solar panel installed on rooftops, ground mounts, or solar parks. We’ll explore technologies, materials, processes, trends, and market leaders to offer a full-circle understanding of this dynamic sector.
What is Solar Module Manufacturing?
Solar module manufacturing is the process of creating photovoltaic (PV) modules, which convert sunlight into electricity. It involves the step-by-step fabrication of solar panels from raw materials like silicon into fully assembled, tested, and ready-to-install modules, ensuring durability and weather resistance.
Core Stages of Solar Module Manufacturing
1. Polysilicon Production
Polysilicon is a high-purity, fine-grained crystalline silicon product, typically in the shape of rods or beads. It is produced using highly reactive gases, primarily metallurgical-grade silicon, hydrogen, and chlorine. The Siemens process involves passing a silicon-hydrogen-chlorine compound gas over a heated silicon filament, breaking molecular bonds and depositing silicon atoms. The hydrogen and chlorine atoms are reused in a closed cycle. Another method involves placing small silicon beads at the bottom of an inverted cone-shaped vessel, where a compound gas of silicon and hydrogen is pumped in, breaking bonds and depositing silicon atoms.
2. Ingot and Wafer Production
Polysilicon is transformed into wafers through various processes, including the Czochralski process and directional solidification. The liquid mass is heated to form a liquid mass, which is then sliced into thin wafers using diamond-coated wire saws. The resulting silicon sawdust, called kerf, is then used to create a wafer. Kerfless wafer production can also be achieved by pulling cooled layers off a molten bath or depositing a thin layer of silicon atoms onto a wafer template.
3. Cell Fabrication
Silicon wafers are fabricated into photovoltaic cells through chemical texturing to remove saw damage and increase light exposure. The process varies depending on the device architecture, with most cell types requiring exposure to an electrically active dopant gas and coating surfaces with layers for improved performance. Screen printing of silver metallization is also common.
4. Module Assembly
Module assembly involves connecting silver busbars in cells using copper ribbons plated with solder. The interconnected cells are arranged face-down on a glass sheet covered with polymer encapsulant, followed by a polymer backsheet or glass. The stack is laminated in an oven for waterproofing, fitted with an aluminum frame, edge sealant, and a junction box. The ribbons are connected to diodes to prevent backward electricity flow. Electrical cables from the junction box convey module current to adjacent modules or power electronics.
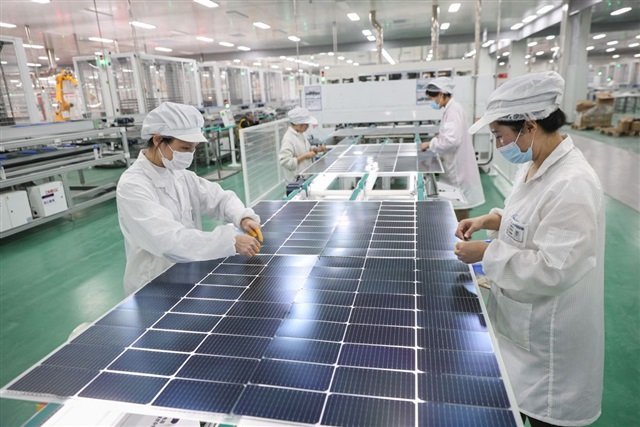
The Importance of Solar Module Manufacturing in the Renewable Ecosystem
1. Powering the Clean Energy Transition
Solar modules are the heart of solar power systems. Without them, there is no solar energy. By enabling the mass production of affordable, efficient modules, manufacturers accelerate the shift from fossil fuels to renewables—helping countries meet their clean energy targets faster.
2. Strengthening Energy Independence
Manufacturing solar modules domestically reduces reliance on imports, shields nations from global price shocks, and strengthens energy security. In countries like India, this supports the Atmanirbhar Bharat (Self-Reliant India) mission by building resilient, local suply chains.
3. Driving Industrial Growth and Employment
Every gigawatt (GW) of solar module manufacturing capacity generates 1,000–1,300 direct jobs. It also supports indirect employment across logistics, R&D, testing labs, maintenance, and installation. Solar manufacturing is becoming a backbone industry for sustainable industrial development.
4. Enabling Innovation and Technological Advancement
Manufacturing is the launchpad for innovations like:
- PERC, TOPCon, and HJT solar cells
- Bifacial and thin-film solar modules
- Smart modules with integrated monitoring systems
Such breakthroughs improve energy yield, reduce costs, and expand the applications of solar—from rooftops to floating solar, to agrivoltaics.
5. Supporting Climate and ESG Goals
Sustainable solar module manufacturing contributes to global climate commitments by reducing the carbon footprint of solar energy production. Manufacturers are adopting:
- Green energy-powered factories
- Lead-free soldering
- Module recycling initiatives
- Water conservation techniques
6. Accelerating Utility-Scale and C&I Deployments
With growing demand in commercial & industrial sectors and utility-scale solar farms, manufacturing must keep pace to supply high-quality panels quickly and cost-effectively. Fast, flexible, and local module production helps projects avoid delays and maintain profitability.
7. Ensuring Quality and Climate Adaptability
Local manufacturing allows customization of modules to specific climate conditions—whether it’s coastal humidity, high temperatures, or desert winds. This increases durability, performance, and the lifespan of solar power systems, especially in challenging industrial environments.
8. Influencing Energy Markets and Policy
As countries ramp up solar deployment, solar module manufacturing becomes a strategic sector. Policies like:
- PLI (Production Linked Incentive) in India
- ALMM (Approved List of Models and Manufacturers)
- Solar import duties
are reshaping trade, investment, and job creation. Manufacturing is no longer a backend process—it’s now central to clean energy policy and global competitiveness.
Key Raw Materials in Solar Module Manufacturing
To understand the intricacies of solar module manufacturing, it’s essential to know the key materials involved:
1. Silicon
Solar cells use semiconductors, which are sliced into thin wafers after purification. They make up over 90% of the global PV market. Monocrystalline is more efficient but expensive, while polycrystalline is cost-effective but slightly less efficient.
2. Glass
Tempered solar glass, typically 3.2mm in size, is a protective front layer for solar modules, offering high transparency and anti-reflective coatings to enhance light capture and protect internal components from weather, dust, and mechanical damage.
3. Encapsulants (EVA or POE)
This protective adhesive layer between glass, solar cells, and backsheet cushions cells, prevents moisture ingress, maintains optical transparency, and provides electrical insulation. High-quality EVA ensures module longevity and performance, with transparent polymer for stability.
4. Backsheet
Multi-layered polymer sheets made from PVF, PET, or PVDF provide electrical insulation and protection against moisture and UV, ensuring module long-term durability and protection from environmental damage.
5. Aluminum Frame
The module’s mechanical strength and support are provided by lightweight, corrosion-resistant materials, which are compatible with standard mounting systems. Copper and aluminum are used in busbars and framing, aiming to reduce costs without compromising efficiency.
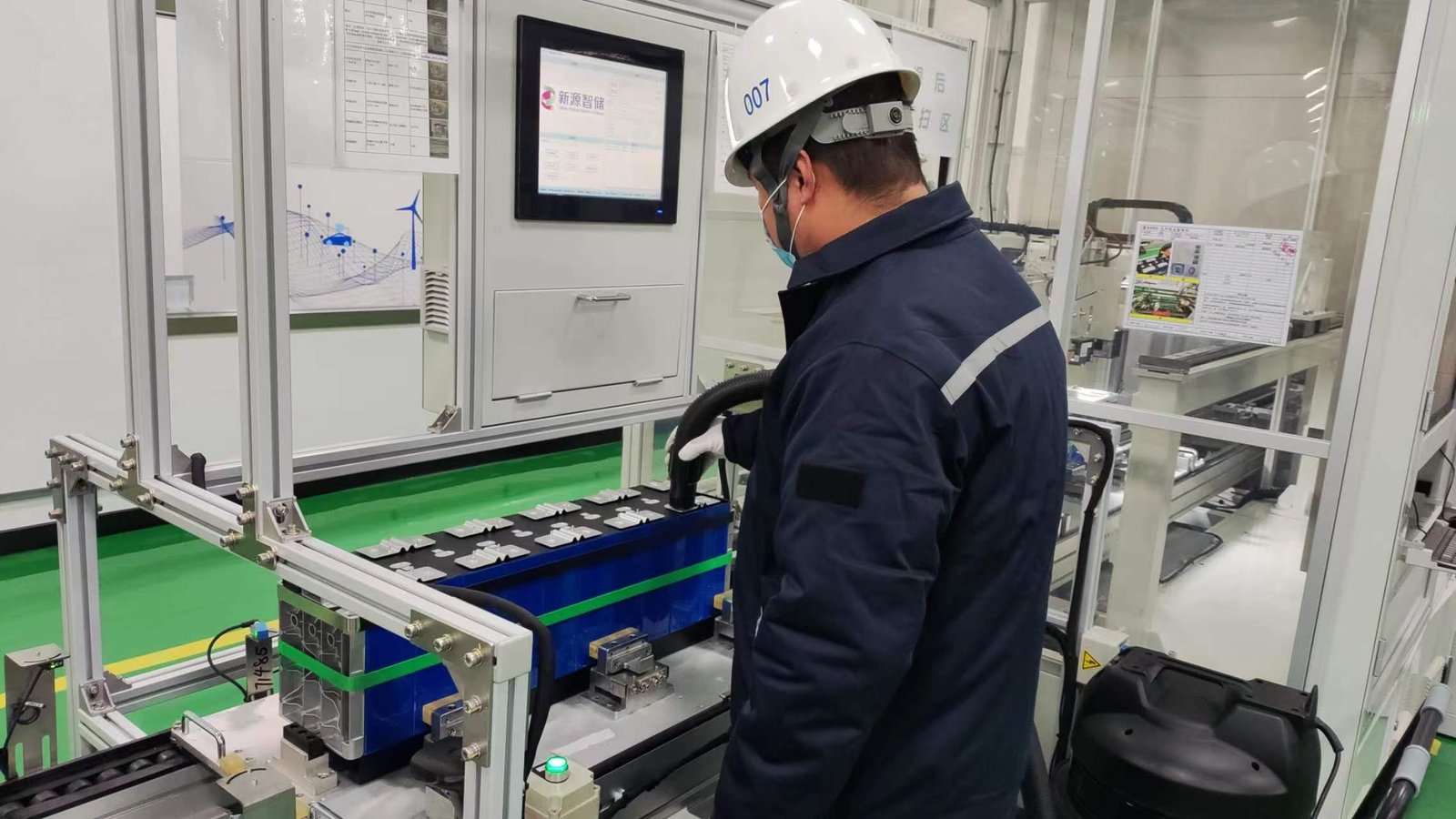
Step-by-Step Process of Solar Module Manufacturing
1. Silicon Purification & Ingot Growth
- Quartzite is heated in electric furnaces to form metallurgical-grade silicon, which is refined using the Siemens process into pure polysilicon. This is then cast into monocrystalline or polycrystalline ingots, often in vacuum systems to eliminate impurities. The process is crucial as impurities reduce efficiency and cause cell degradation. The goal is to form solid blocks of pure silicon crystals, with monocrystalline grown using the Czochralski process and polycrystalline formed by casting molten silicon into square molds.
2. Wafer Slicing
- The process involves cutting ingots into ultra-thin wafers using diamond-coated wires, resulting in clean, smooth wafers ready for solar cell processing. Thinner wafers reduce material use and costs, while acid-etching removes saw damage and enhances light absorption.
3. Solar Cell Fabrication
- Electricity generation involves doping wafers with phosphorus or boron to create p-n junctions, which are essential for current flow. Texturing and anti-reflective coatings like silicon nitride enhance light capture. Metalization involves silver paste for front contacts and aluminum or copper for rear. Screen printing is done with silver paste for front contacts and aluminum for back, followed by high-temperature treatment for solidifying metal contacts.
4. Cell Testing and Sorting
- The objective is to test electrical characteristics such as open-circuit voltage, short-circuit current, and efficiency in a module. Cells are sorted by performance to ensure uniformity, as mixing different grade cells can lower efficiency.
5. Cell Interconnection (Tabbing/Stringing)
- Solar panels consist of solar cells interconnected in strings using copper ribbons through manual or automated soldering. The layout typically includes 60-cell, 72-cell, or 144 half-cut-cell configurations, with good interconnection minimizing electrical loss.
Technologies in Solar Module Manufacturing
Modern solar module manufacturing leverages advanced technologies to improve yield and performance:
1. PERC, TOPCon & HJT Cell Architectures
The Passivated Emitter Rear Cell (PERC) enhances light capture and efficiency by 22-23%, while TOPCon and HJT cells increase efficiency by 28-30%, enhancing energy yield in C&I projects. These technologies, widely adopted globally, improve cell performance without significantly increasing costs, making them the most widely adopted tech globally.
2. Bifacial Modules
Biacial panels capture sunlight from both front and rear sides, boosting energy yield by up to 30%. Ideal for ground-mounted, floating solar, and carport installations, they capture both direct and reflected sunlight, enhancing yield by up to 30% in high-albedo settings. Floatovoltaics use cooling water bodies to increase efficiency and conserve land.
3. Automation, AI & Digital Twin Manufacturing
Modern factories employ AI/vision robots, cleanroom environments, and materials-handling systems to minimize micro-cracks and defects. Digital twins simulate production lines, enabling predictive quality assurance and reducing rework. Technologies include automated material handling, precision laser cutting, vision systems, and AI-based quality assurance.
4. Flexible & Thin-Film Innovations
Roll-to-roll CIGS thin-film modules, like Flisom, produce lightweight, flexible panels for BIPV and mobile applications. Inkjet-printed perovskite cells enable fast, low-cost solar production. Solar modules deployed on water bodies reduce land use, minimize heating, and improve efficiency.
Sustainability in Solar Module Manufacturing
Sustainability in solar module manufacturing is becoming a necessity as the demand for clean energy grows. Leading manufacturers are increasingly using recycled materials like silicon, glass, and aluminum, reducing their dependency on virgin resources. European companies have managed to recover up to 95% of materials from decommissioned solar panels. Design innovations, such as recyclable backsheets and frameless modules, promote a circular economy.
Manufacturing facilities now operate on clean, renewable power sources like solar and wind energy, contributing to a significant reduction in operational emissions. These factories often adhere to international certifications such as ISO 50001, demonstrating commitment to energy efficiency and reduced carbon output. Water usage is optimized through closed-loop and zero-liquid-discharge systems, and innovative cleaning techniques minimize the use of water and chemicals during production.
Advanced recycling technologies allow for the recovery of critical materials with up to 99.3% efficiency, using as little as 1 kWh per panel. Modern solar factories leverage robotics, artificial intelligence, and digital twins to ensure lean production and reduce production waste by over 30%.
Certifications and compliance with regional and international standards are key indicators of sustainability in manufacturing. Opting for sustainably manufactured solar modules helps companies reduce their Scope 3 emissions, strengthens ESG performance, and aligns with global climate and compliance goals.
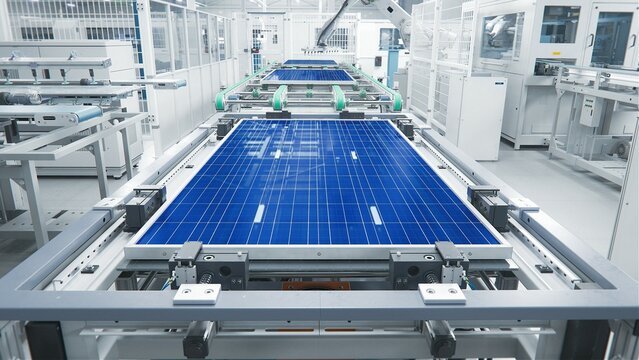
Solar Module Manufacturing in India: Opportunities and Growth
India is rapidly emerging as a global hub for solar module manufacturing, fueled by progressive policies, rising domestic demand, and a strategic vision of becoming self-reliant in clean energy. With over 300 sunny days a year and a national commitment to achieving 500 GW of non-fossil fuel capacity by 2030, the country is firmly positioned at the forefront of a clean energy revolution. Over the past few years, India’s solar module manufacturing capacity has seen exponential growth, led by major players such as Adani Solar, Waaree, Vikram Solar, RenewSys, Tata Power Solar, and the Reliance Giga Complex—all actively investing in state-of-the-art production lines.
The Indian government has played a catalytic role in this transformation, with the landmark Production Linked Incentive (PLI) Scheme committing ₹24,000 crore across two phases. Designed specifically to support integrated solar module manufacturing—from polysilicon to modules—the scheme aims to create 48 GW of capacity by 2026 and has already attracted ₹41,000 crore in private sector investment. Additional policy initiatives, including the Basic Customs Duty (BCD) of 40% on modules and 25% on cells, the Approved List of Models and Manufacturers (ALMM), and the development of Solar Parks and SEZs, further strengthen India’s solar module manufacturing ecosystem.
India’s emergence as a trusted alternative in the global solar supply chain is already evident, with exports to the United States alone crossing $1.8 billion in FY 2024. Today, Indian solar module manufacturing is evolving from simple assembly lines to centers of innovation. Manufacturers are adopting AI-driven automation, robotics, and next-generation technologies like HJT, TOPCon, and bifacial panels. There is also a growing focus on recyclable, eco-friendly module designs and indigenous R&D for higher efficiencies and cost optimization.
Looking ahead, industry forecasts predict that India’s solar module manufacturing capacity will exceed 125 GW by 2029—well above projected domestic demand—unlocking new opportunities for export-led growth. However, to achieve full energy independence, the nation must also scale upstream capabilities, transition to renewable-powered factories, develop a highly skilled workforce, and establish robust international logistics infrastructure.
Challenges in Solar Module Manufacturing
1. Upstream Supply Chain Dependency
- India’s heavy reliance on imports for upstream materials like polysilicon, ingots, wafers, and cells, primarily from China, weakens supply-chain resilience and exposes manufacturers to geopolitical risks, price volatility, and trade restrictions. This lack of domestic capacity for critical raw materials, including “Made-in-India” modules, undermines supply chain resilience and exposes manufacturers to global price fluctuations.
2. High Capital Costs for Vertical Integration
- The cost of solar modules, including cells, is significantly impacted by fluctuating prices for materials like wafers and EVA, along with inefficient inventory management. Developing fully integrated solar manufacturing facilities requires significant capital investment, limiting the number of vertically integrated players in India, slowing down the Atmanirbhar Bharat vision.
3. Technology Gaps & R&D Deficit
- Indian manufacturers are lagging in advanced technologies like TOPCon, HJT, and bifacial cells due to limited in-country R&D and innovation capabilities. Most advanced tech is imported or licensed, hindering cost-competitiveness and self-reliance. The lack of investment in local innovation, testing infrastructure, and talent development restricts India’s ability to create next-gen modules independently.
4. Energy Intensity & Power Costs
- India’s high industrial electricity tariffs, particularly in polysilicon purification and wafer slicing, make solar cell production highly energy-intensive, making it difficult to achieve price parity and sustainability in the industry. This is due to the lack of reliable access to low-cost, clean energy.
5. Logistics, Infrastructure & Land Acquisition
- Manufacturing plants require logistics support, including well-connected ports, reliable land, water, and power. Acquisition delays and state-level regulations disrupt timelines and increase costs. Indian industrial zones are developing these essentials, and bureaucratic delinquency hinders their development.
6. Talent & Workforce Shortage
- India faces a skills gap in advanced solar manufacturing, particularly in precision manufacturing, robotics, and semiconductor-grade material handling due to a lack of specialized training institutes and R&D collaboration between industry and academia, and a lack of training infrastructure for downstream and upstream processes.
Future Trends in Solar Module Manufacturing
The solar module manufacturing industry is experiencing a significant technological revolution, with companies like First Solar and UbiQD developing copper-indium quantum dot coatings to enhance energy output from reflected light. New cell architectures like TOPCon, Heterojunction, and perovskite-silicon tandem cells are pushing module efficiencies to unprecedented levels. Design evolution is also transforming solar modules, with bifacial modules being increasingly adopted in utility-scale and ground-mounted systems. Building-integrated photovoltaics (BIPV) is leading to transparent and aesthetic modules that blend into building facades, skylights, and windows.
Automation, artificial intelligence, and digital twin technologies are reshaping solar manufacturing lines, improving yield, reducing costs, and shortening production timelines. Cooling innovations and material substitutions are also gaining traction, with passive cooling systems and phase-change materials managing thermal loss and copper-based contacts reducing dependence on costly materials. Localized and modular manufacturing plants are being developed across regions to decentralize production and create resilient supply chains. The solar industry is expanding its footprint through flexible modules and floating solar farms, offering more efficient, durable, and customizable solar solutions.
Why Choose Soleos Solar for Solar Module Solutions
At Soleos Energy Private Limited, we stand at the forefront of India’s clean energy revolution by delivering trusted, high-performance solutions powered by the latest in solar module manufacturing. With over 12 years of experience and a strong presence across India, Europe, the UK, UAE, and Africa, we partner with industry-leading manufacturers who specialize in cutting-edge solar module manufacturing technologies like TOPCon, HJT, and bifacial panels. Our global clients benefit from efficient, durable, and environmentally responsible modules designed to meet the unique demands of commercial and industrial applications.
As the demand for quality and speed grows, our deep integration with India’s rapidly growing solar module manufacturing ecosystem allows us to offer faster delivery, superior technical support, and complete compliance with green certifications. Whether it’s for ground-mounted projects, rooftop installations, carports, or agrivoltaics, Soleos ensures every project is powered by the excellence of advanced solar module manufacturing—driving energy efficiency, ROI, and sustainability for your business.
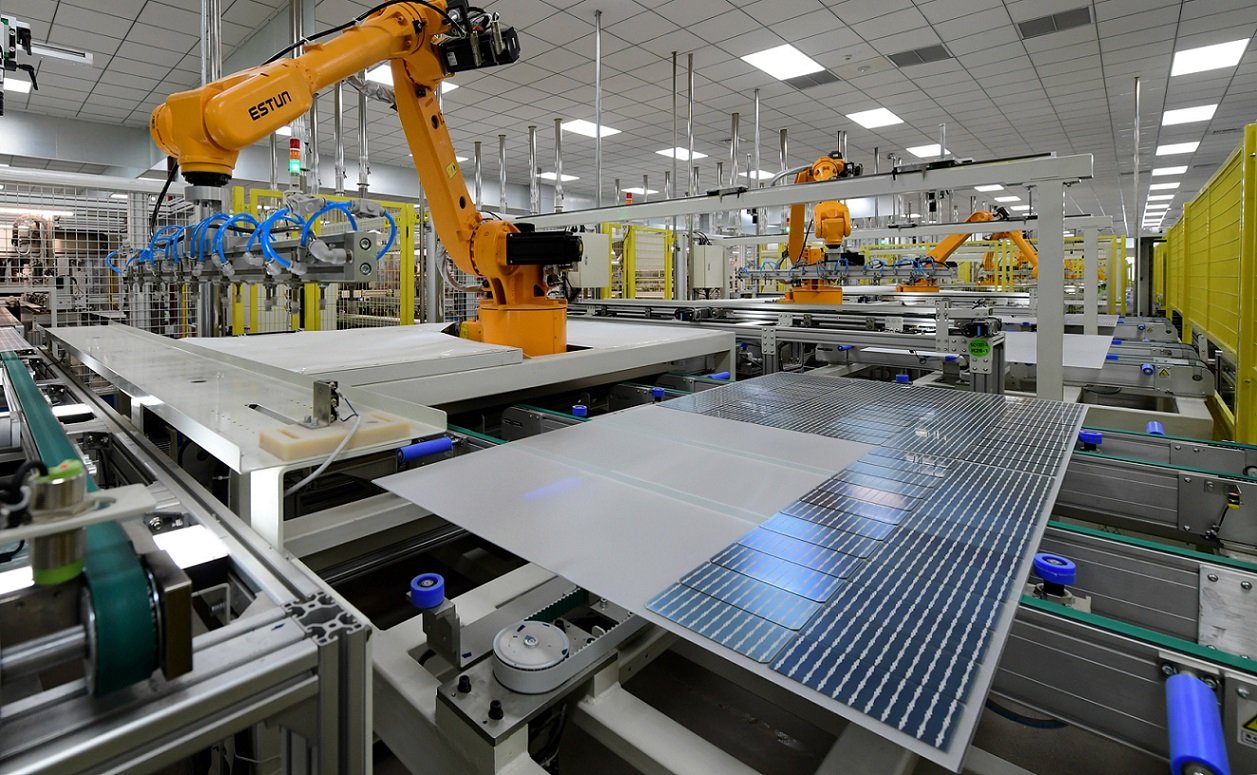
Government Initiatives Supporting Solar Module Manufacturing
The Indian government has implemented a proactive policy ecosystem to accelerate solar module manufacturi ng, aiming to reduce import dependence, spur economic growth, and meet climate targets. Key initiatives include:
1. Production-Linked Incentive (PLI) Scheme
Launched in two tranches, the PLI scheme is a cornerstone effort to bolster solar module manufacturing.
- Tranche I (₹4,500 cr) and Tranche II (₹19,500 cr) allocate incentives to developers of integrated solar PV modules, covering polysilicon, wafers, cells, and module production.
- Under Tranche II, nearly 39.6 GW of domestic module manufacturing capacity has been sanctioned, supported by ₹14,007 cr investment, and expected to generate over 100,000 jobs.
- This initiative reinforces India’s push to become self-reliant in solar module manufacturing, reduce yearly import bills by ₹17,500 cr, and achieve economies of scale .
2. Basic Customs Duty (BCD) & Domestic Content Requirements
- A BCD of 40% on modules and 25% on cells, later reduced to 20% each in the 2025–26 Union Budget, shields domestic manufacturers from cheaper imports.
- Alongside Domestic Content Requirements (DCR) and the Approved List of Models and Manufacturers (ALMM), these policies mandate the procurement of domestically produced solar PV modules and cells for public clean-energy projects.
3. National Solar Mission & MNRE Schemes
- India’s National Solar Mission, launched in 2010, set initial targets for solar capacity and laid the foundation for large-scale solar parks and manufacturing ecosystems.
- Ongoing MNRE schemes—such as the PM Surya Ghar Muft Bijli Yojana, Pradhan Mantri Kisan Urja Suraksha evam Utthaan Mahabhiyaan (PM-KUSUM), and central PSU initiatives—farm-in procurement policies that prioritize India-made modules and cells, driving local demand.
4. Infrastructure & Sectoral Support
- Investments in solar parks, SEZs, and logistics improvements (including PM GatiShakti initiatives) support streamlined land acquisition and supply chain efficiency.
- Financial backing from agencies like IREDA provides loans and grants specifically for solar module manufacturing projects
Conclusion
India’s journey in solar module manufacturing is entering an exciting new phase. With over 70 GW of module capacity now installed—up from just 2 GW a decade ago—thanks to game-changing government initiatives like the PLI scheme, Basic Customs Duty adjustments, and infrastructure support, India is emerging as a formidable clean energy force. Major investments, such as SAEL’s ₹8,200 cr mega-facility in Greater Noida to produce 5 GW of cells and modules annually, further underscore India’s commitment to self-reliance and global competitiveness.
However, to fully realize India’s clean energy potential, it’s essential to address critical challenges like dependence on upstream imports, high energy costs, and skill shortages. With combined efforts from policy, industry, and innovation, these bottlenecks are being tackled to build a resilient and future-ready solar manufacturing ecosystem.
Soleos Energy offers Next-Gen solar PV solutions manufactured in India, aligned with PLI incentives and green energy mandates. Equipped with high-efficiency technologies, these solutions are supported by local logistics and technical service. Partnering with Soleos ensures commercial or industrial projects utilize India’s solar module manufacturing boom’s full potential.